The highly complex and sensitive nature of combustion makes it one of the most challenging processes to control regularly and reliably in industry. Hybrid artificial intelligence and expert knowledge capture make the difference when it comes to achieving real and lasting improvements. Taber International's Combustion Optimization System (COS) built within the Griffin AI Toolkit® platform recognizes that all units are distinct and custom builds each application to meet the specific needs of every unique unit.
We customize each COS application to fit the unique traits and requirements of the system and unit we're focusing on. By blending machine learning with captured expert knowledge from site engineers and operators, we can optimize various goals simultaneously. Plus, our system can adapt in real-time to prioritize different goals based on current conditions.
We have successfully simultaneously optimized:
- NOx Emissions (10%-40%) and CO Emissions (40%+)
- Heat Rate Improvement (0.7%-1.5%)
- Temperature Control (swings reduced 25%+)
- Tube Metal Temperatures (exceedances decreased by 80%+)
- Loss-on-Ingnition (LOI) / Carbon-in-Ash (CIA)
- Boiler Slagging of Tube Sections
As an adaptive, intelligent solution, Taber's COS is compatible with a wide variety of equipment and unit configurations.
- Tangentially-fired, wall-fired, or cyclone units
- Forced or natural circulation
- Sub-, super-, and ultra-supercritical units
- With or without low NOx burners
- Works in concert with SCRs or SNCRs, if present
- Few or many automated hardware components
NOx and CO Emissions
MATS Rule and EPA Clean Air Act Title V regulations require that power plants take steps to reduce and optimize their emission rates of certain pollutants.
One of the most cost-effective methods of realizing this is through a real-time combustion optimization system.
Taber's COS has been implemented at numerous sites and all major unit types (e.g., T-fired, wall-fired, cyclones) for NOx and CO control and reduction and has seen tremendous success, with results ranging from 20%-40%+ NOx reductions and 40%+ improvement in CO emission rates.
One long-term study demonstrated continual improvements in observed NOx emission rates quarter-to-quarter, ultimately achieving an average improvement of 22.5% across the unit's load range.

Heat Rate Improvement

A typical unit implementing Taber's COS for Heat Rate improvement will see, on average, a 0.7% - 1% improvement, while improvements in excess of 1.5% have been realized.
The COS improves the heat rate through more efficient overall combustion and energy utilization, resulting in lower controllable losses such as lower average excess O2, reduced spray flow, and lower auxiliary power usage.
Heat rate improvements across the load range are achievable, often with the greatest opportunity at low- and ultra-low loads as units become more flexible to meet ever-changing grid demand.
Temperature Control
Increased unit flexibility to meet challenging grid demands has placed an emphasis on improved temperature control through combustion units. Maintaining consistent temperatures below limits increases unit health and reliability, decreasing maintenance costs and improving overall performance, contributing to efficiency improvements and unit dispatch order.
Steam temperatures across the unit's load range are more consistent, and improved temperature setpoint realization is achieved. This is espeically important at low- and ultra-low loads where heat rate often suffers.
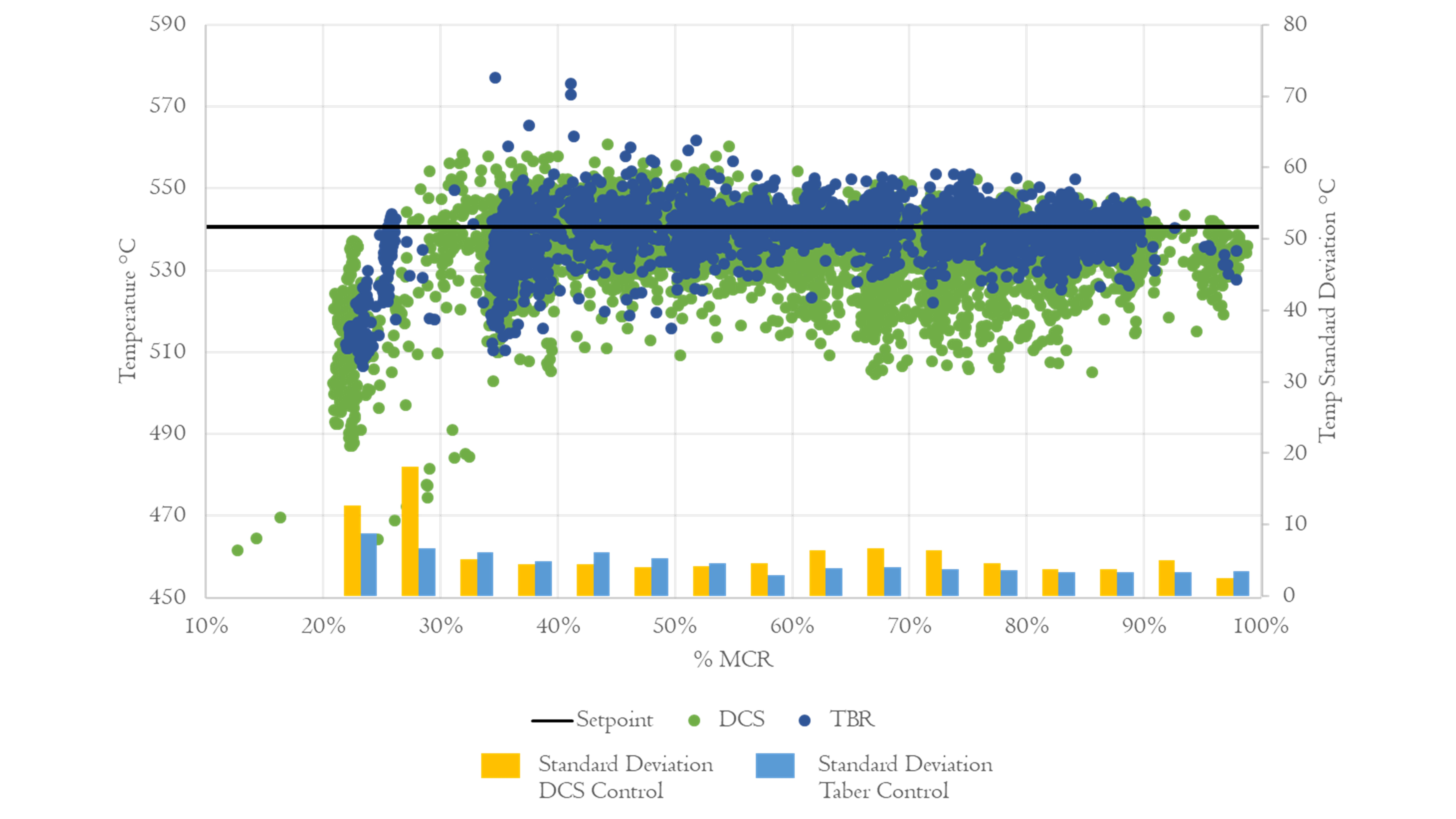
Self-Learning and Self-Adapting
The artificial intelligence deployed within the combustion optimization system learns the unique relationships between all the operating parameters of the unit, recognizing best practices for optimal performance in the current unit situation. The system is also configured to learn and update itself in real-time, meaning that as the unit changes over time (e.g., equipment degradation), the system is automatically learning the effects this has on the unit and adapting its decision-making in response. Sites have even been able to avoid the installation of SCRs through the NOx emission improvement performance achieved using real-time combustion optimization. "Using the Griffin system, Ameren has been able to meet our NOx targets without the installation of any SCR’s on our 10 coal-fired boilers. By purchasing the Griffin SW corporate license, we have saved millions of dollars in optimizer license fees compared to previous optimizers that were purchased by Ameren.”achieved using real-time combustion optimization." - Tom Ziegler, Principal Engineer, Ameren Services
Expert Knowledge Capture
One of the most unique features of Taber’s Combustion Optimization System is the ability to rapidly integrate the knowledge of experienced operators and engineers at the site. Through close collaboration, operational best practices are identified by those who know the system the best – site personnel – and these practices are directly integrated into the control structure of the COS. Automation of these best practices ensures the system is adequately prepared to take action immediately to respond to various events, just as the best operators would – fast and smoothly, avoiding excursions and process upsets. This knowledge capture also ensures that as experience retires, knowledge and experience is retained and that it continues to benefit the site for years to come.