Cooling towers are an integral piece of equipment for many processes, from power generation to food processing. Such systems which utilize fans to create draft (both forced and induced) can use a substantial amount of power, representing higher operating costs or decreased operating efficiency.
Minimize Power Usage and Maximize Cooling Effect
Although on the surface, cooling towers may appear simple with little opportunity for performance changes beyond a rebuild, this is not the case. Ambient conditions (e.g., temperature, humidity, wind speed and direction, etc.) have a dramatic effect on the system’s behavior, and can even affect efficiencies from cell to cell. Compound this with variable cooling demands caused by changing process conditions, and there are many interactions that need to be accounted for in cooling system operation. Intelligent systems can learn to understand these multiple factors and their influence, thereby identifying how to adapt to these to keep the system operating as efficiently as possible.
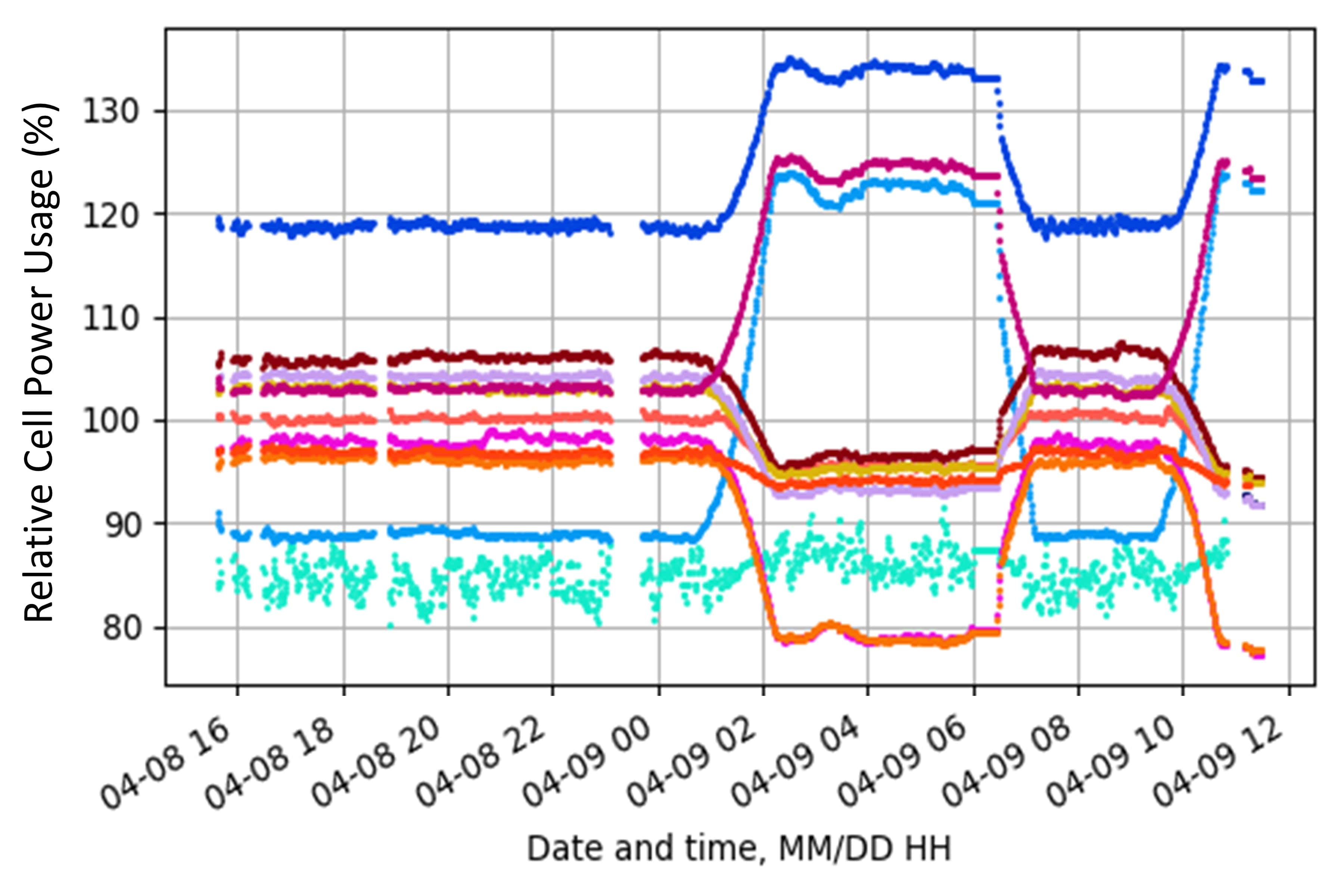
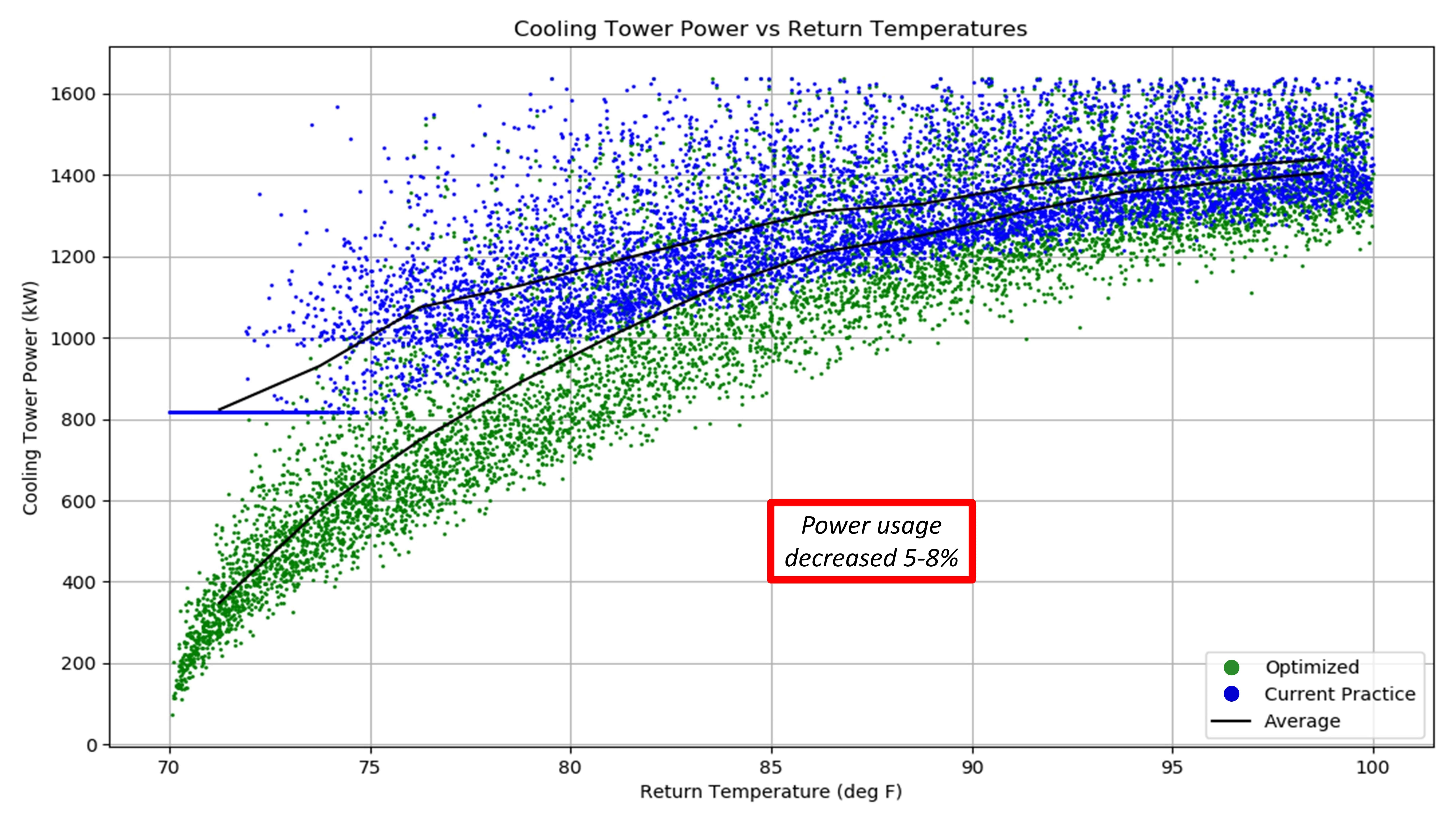
Taber’s Cooling Tower Optimization application (CTopt) can reduce power consumption while achieving similar or even improved process performance. Intelligently balancing tower power demand and active tower cells with cooling demand and outlet temperatures ensures that process cooling needs are met at the lowest achievable cost. CTopt has demonstrated power consumption reductions of 5-10% while maintaining outlet temperatures through intelligent control of individual fan speeds. The system is also effective in prioritizing cell activation and deactivation orders when only on/off control ability is available so that the most cost-effective cells are always operating and are transitioned at the most optimal time.
Installation of Griffin Open Systems® AI platform and Taber’s CTopt application is quick and simple, requiring less than one week after internal control system changes are in place. Necessary I/O points are minimal, needing less than 50 I/O points depending on system size and scope. After a short AI learning and exploratory period (typically 2 – 3 weeks), benefits of the optimization system can be expected to be seen within one month of install.
Observed Benefits on a Real-System
Deployment of Taber's cooling tower optimization system has realized benefits in power consumption and secondary benefits in water consumption across the tower's load range, in this case at a power generation facility. This is a multi-cell induced-draft cooling tower equipped with VFD controls on each individual cell's fan motor. The system takes advantage of the individual VFDs, adjusting fan speeds to capitalize on utilizing the most efficient cells for current ambient conditions, and adapting to real-time changing condiitons (wind speed, temperature, humidity, etc.)
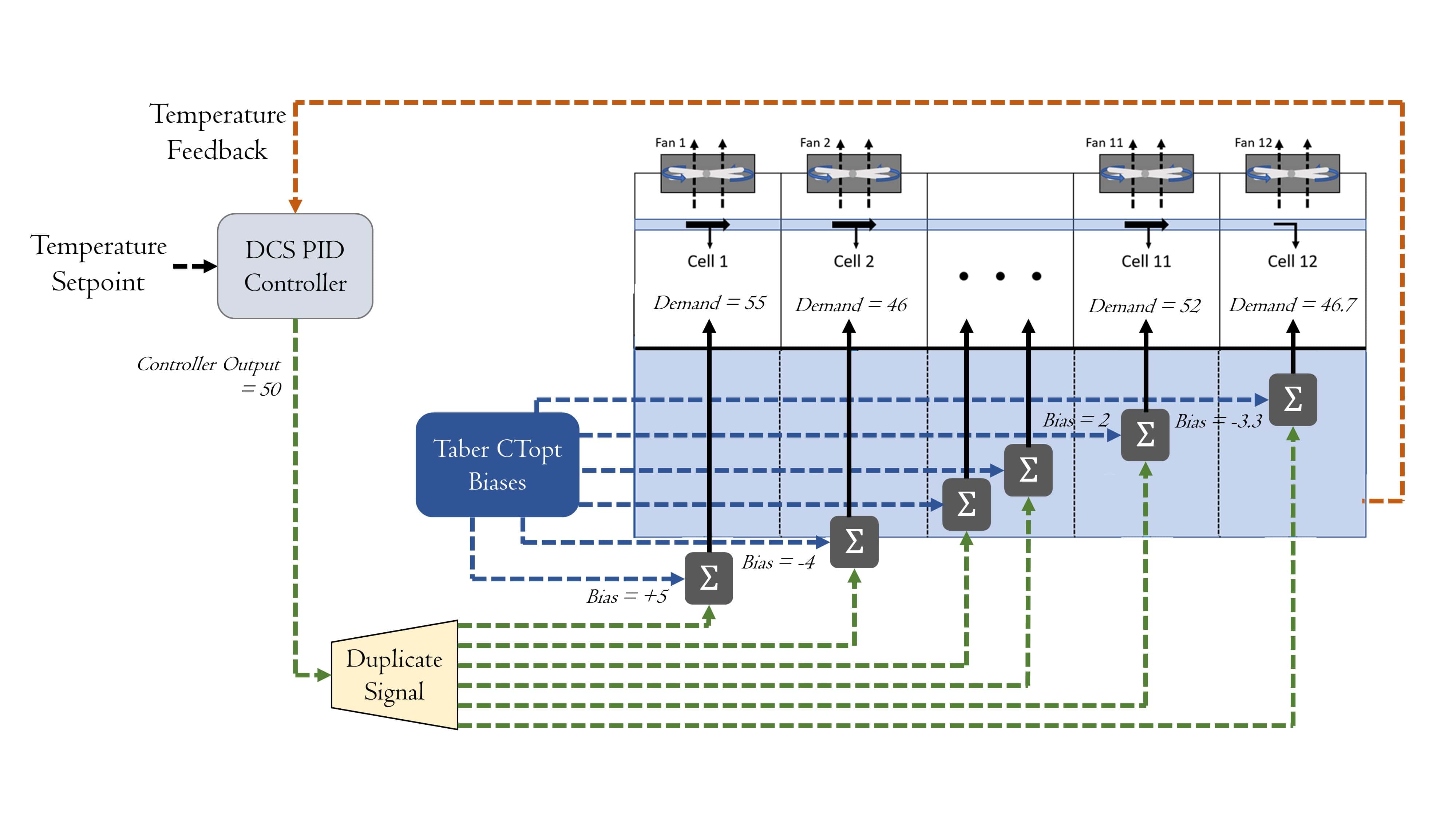
In this case-study, optimization realized on average a 7.7% reduction in tower power consumption and a 3.91% reduction in water consumption during the 6-month analysis period, running through summer and winter to capture both seasonal extremes. At some loads, the higher priority of maintaing system cooling demand was seen to dominate performance optimization, which was a positive observation for the client, confirming that the main objective and purpose of the tower would not be compromised.
This approach of cooling tower optimization is also applicable to different tower structures, with or without VFD equipment. The implementation method will be adjusted accordingly to capitalize on the conditions of the subject process.
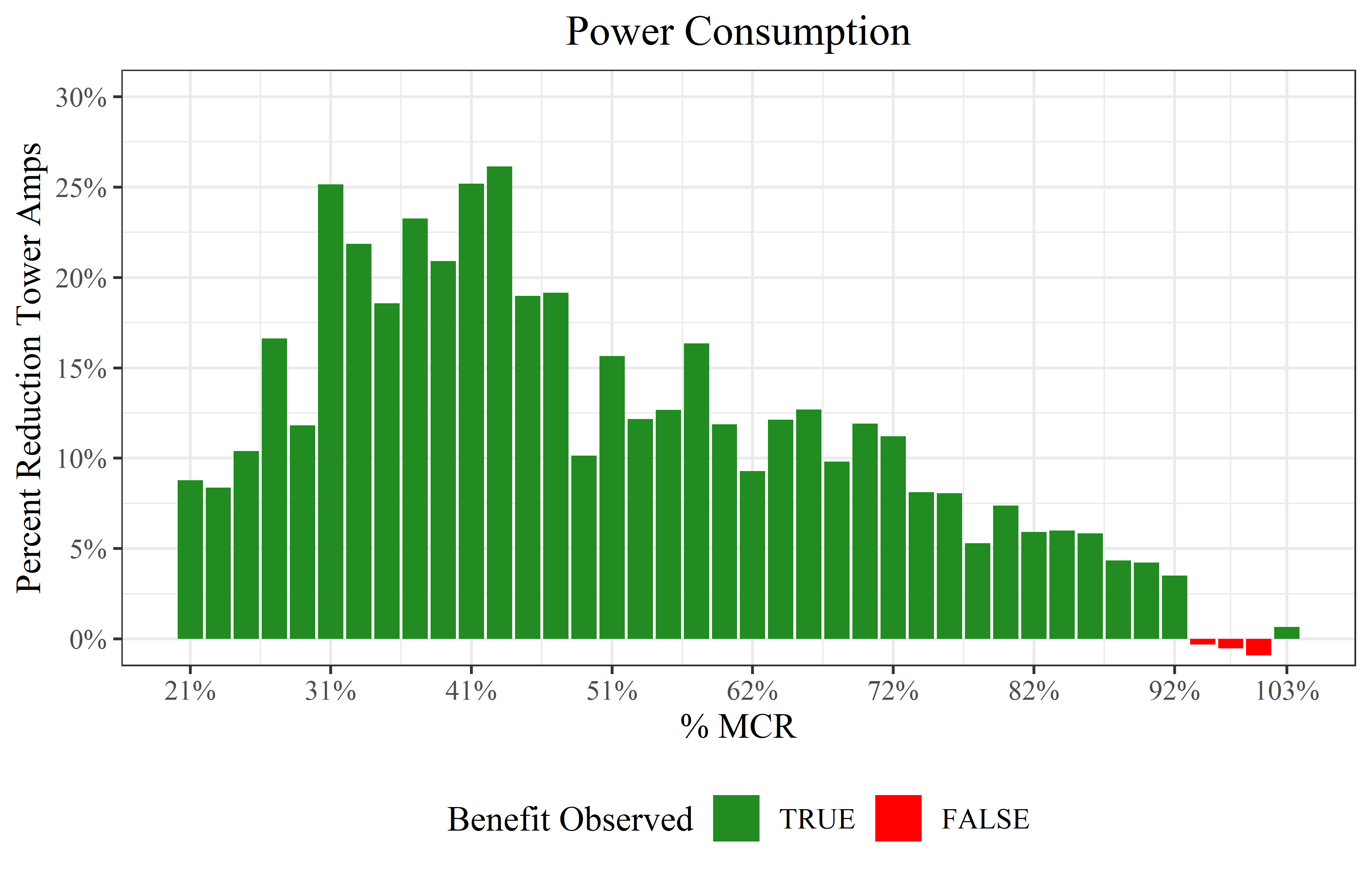
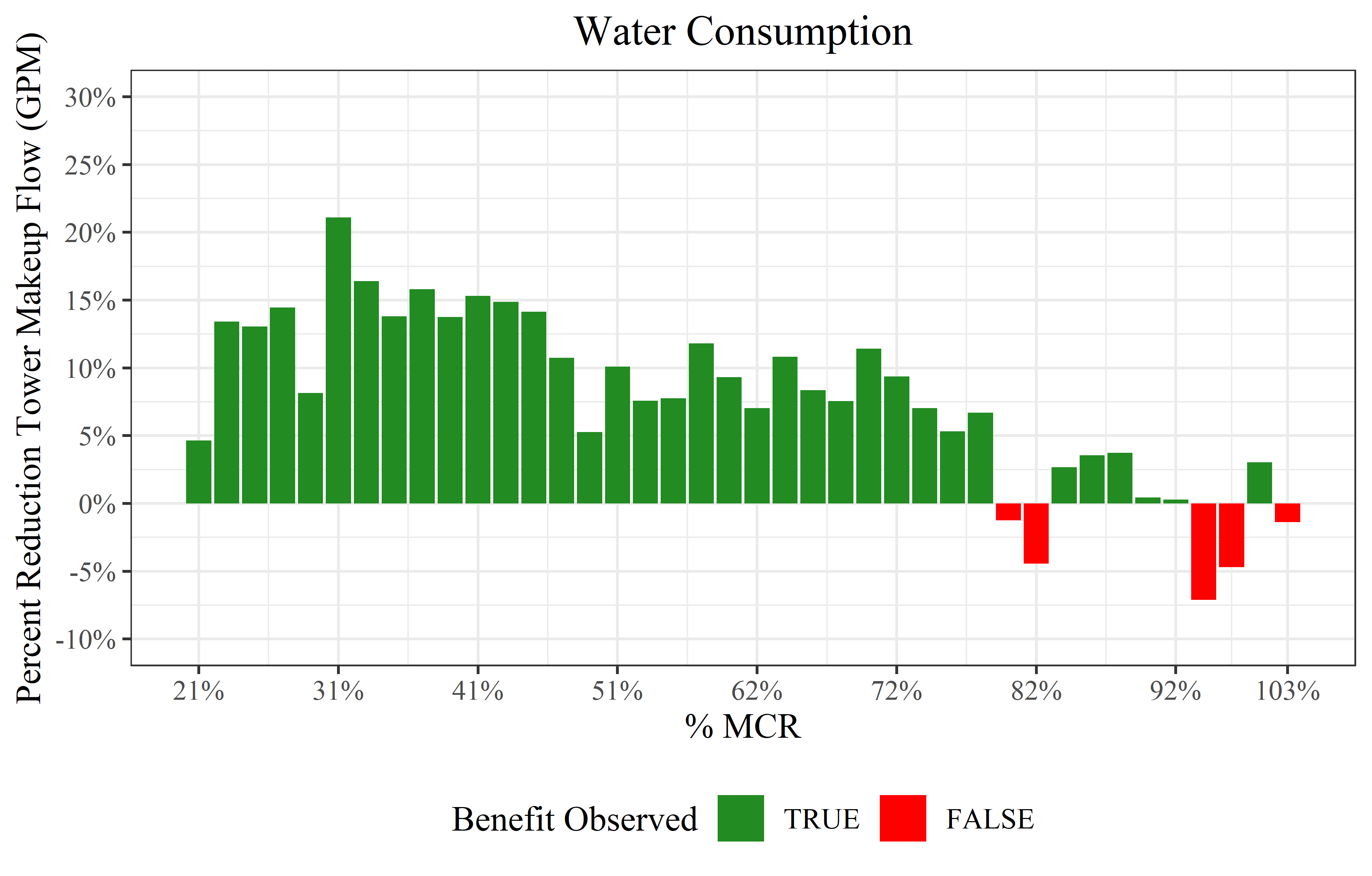
optimize the complex, automate the mundane
talk to an expert